- Produits
- Systèmes
- Capteurs
- Logiciels
- Accessoires
- Integration
ZEISS #measuringhero Award
Winner of the Category: Smoothest Surface & Outstanding Application – Smallest Component
Nobby Assmann from the Netherlands won twice the #measuringhero Award - in 2020 and 2021.
With an Ra-value of 0.00054 µm (0.02 µin) and an Rz-value of 0.0031 µm (0.12 µin), Nobby from Assmann Verspaningstechniek V.O.F. has measured the smoothest surface of all participants in 2021. His smoothest surface is a little disc made of hardened steel used for testing coatings, with a diameter of 16 and a thickness of 3 millimeters. "I love measuring. Lapping and polishing is another passion of mine. Making a dull piece of steel shine like a mirror is very addictive!", he says. The disc was measured optically with a ZEISS LSM in the ZEISS Quality Excellence Center in the Netherlands.
He was also able to achieve the outstanding performance of a tiny plate of 0.0048 mm³ and became the #measuringhero in 2020 in the category “Outstanding Application - Smallest Component”. This plate is part of a hearing aid that he manufactured in his precision workshop, which he runs together with his family.
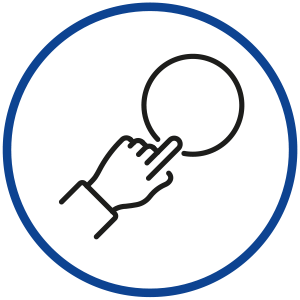
Nobby Assmann
- Company: Assmann Verspaningstechniek V.O.F.
- Industry: Precision manufacturing and metrology
- Country: Netherlands
- My passion for quality assurance: I love metrology!
- Favorite ZEISS product: ZEISS VAST XT head by far! …oh, and the ZEISS CONTURA, ZEISS PRISMO, ZEISS XENOS & ZEISS LSM-900 Microscope
- Why ZEISS: To me ZEISS means quality without any compromises. That’s not only the way I work, it's who I am.
- Your message to the global #measuringhero community out there: Thank you so much for the support. I would love to meet you all and talk about metrology!

What are your daily challenges in metrology?
It’s not so easy to polish surfaces to extremely low roughness heights. It might be even harder to measure the exact surface roughness. Normal measuring devices have a diamond stylus that scan the surface. Those devices can’t measure these highly polished surfaces – so I used a confocal laser scanning microscope. It’s at my nearest ZEISS Quality Excellence Center. The ZEISS LSM 900 Mat does an excellent job measuring every roughness value (S and R) you may need! It’s a real pity I don’t own one yet. I really want one!
What role does surface analysis play in your daily work?
I perform edming, grinding, honing, lapping and polishing for my customers. It is very important that parts are shipped with the correct roughness. That's what my customers pay for.
How did you manage to make the surfaces of the disk so extremely smooth?
I first cut the disk from hardened tool steel by wire EDM. Then I did some surface grinding to improve surface roughness and flatness. The surfaces have been improved with 2 stages of flat lapping and 2 stages of additional polishing. The real magic happened with the last step: CMP. Chemical-mechanical planarization. This is polishing with an aggressive liquid that etches the surface during polishing.

What fascinates you about metrology?
Metrology shows how difficult manufacturing can be. It unveils all the problems a product may have. Some products seem okay and may even be within tolerance using hand measuring tools. It amazes me what I can discover using my ZEISS CONTURA. The ZEISS VAST XT head places a big role in this: a true marvel! I love finding difficult problems and presenting them in an understandable way. ZEISS CALYPSO software allows me to do that.
What challenges did you face in measuring such a small component?
Clamping the part was the first challenge. The second challenge: being able to see the part so that I could take the first few points using the joysticks.
How did you overcome these challenges?
I made a special clamp for the tiny part (0.4 x 0.4 x 0.03 mm). The clamp could hold the delicate part but also allowed access to the part for the spherical probes. To see the part I placed a stereo microscope on the table of the CMM. Just so I could see the part and take the first points with two 0.3 mm probes. After those first points, the CMM did the rest: CNC scanning and probing, just like measuring a larger part.
